Heating linings for galvanic vats
Description: These heaters are placed inside porcelain, titan or quartz-glass tubes, equipped with protective caps and cables. The type of tube depends on the material to be warmed up. Before selecting the material of the protective tube, a common consultation is recommended on the composition of the chemicals that may contact the heater. The upside of these heaters is that it enables ceramic cartridge to be substituted with heating spiral without changing the protective tube.
Use: Heating of different liquids, surface treatment, degreasing and different chemical and electro-chemical processes. Heaters are immersing directly into the given liquid.
Characteristics:
- The biggest advantage of porcelain coating is long-life. Aluminum-oxide can be found in large quantities, which makes it more resistant against the repetitive temperature change. The material of the protective tube (AISI 3I6TI, AISI 3I6L, AISI 304) ensures durability even in aggressive environments too.
- Titan heaters are especially fit for electro-chemical processes, e.g.: nickel or copper coating. They resist mechanical damages and tolerate well if they are working dry for a longer time.
- Heaters made of quartz-glass are used in phosphating chemical- and acidic environments for nickeling and polishing. Incrustations and condensations don’t arise on the surface of glass tubes. The reason for this is that most of the heat radiates from the heater to the heated environment, so the glass tube remains cold.
Practical observations: The following recommendations are only general ones.
- Glass and porcelain tubes are the most resistant to acidic environment. Except for hydrochloric acid, for what teflon tube is the only resistant.
- For alkaline environment, stainless and titan tubes are the proper ones.
- Teflon heaters are the most resistant to corrosive materials, but are sensitive for dry working environment, for shocks and for high temperature. Therefore teflon heaters are only used with fluorinated tubs.
- Operation in a dry environment even for a short time can cause damage in teflon, glass and porcelain heaters. For this purpose, the best fits are stainless and titan-coated protective tubes.
- Glass, porcelain and teflon-coated tubes are sensitive to shocks. Stainless and titan-coated protective tubes are resistant against shocks and mechanical effects.
- Hydrochloric acid and nitric acid damages stainless and titan-coated tubes.
- The use of glass-coated heater is recommended for phosphate tubs.
Installation:
- Filament must be installed vertically, a bit further from the edge of the tub, so the liquid can circulate freely.
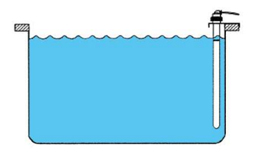
- The heated part of the heater must be in the fluid. (The heated part is marked with a line on the protective tube.)
- The protective cap can never immerse into the fluid and the level of the fluid must be at least 50 mm above. If the tub is covered, a hole must be cut out, where the protective tube can be inserted It is important that the protective cap is above the cover.
- The protective cap and the wire (cord) can only be exposed to max. 70 °C.
- Before connecting it to an electric network, the heater’s electric characteristics must be checked, so that they are proper for the given network. The electric resistance and insulation resistance has to be measured, if necessary.
- When changing the ceramic lining or the network cable, pay attention to the grummet’s placement, so that it ensures the proper seal and avoiding the liquid from entering the inside of the heater.
- It is forbidden to take the filament out of the liquid while it’s still hot. Before taking it out, it is important that the heater is switched off for at least 5 minutes. In the absence of that the filament may burn out, or even start a fire, if there are any flammable materials nearby.
- It has to be checked regularly, that there isn’t any burnt material stick to the heater’s tube. It is recommended to clear the heater from burnt materials from time to time, ensuring a longer life by this too.